Blog
- Home
- Blog
- technical explanation
- Food grinder maintenance
Food grinder maintenance
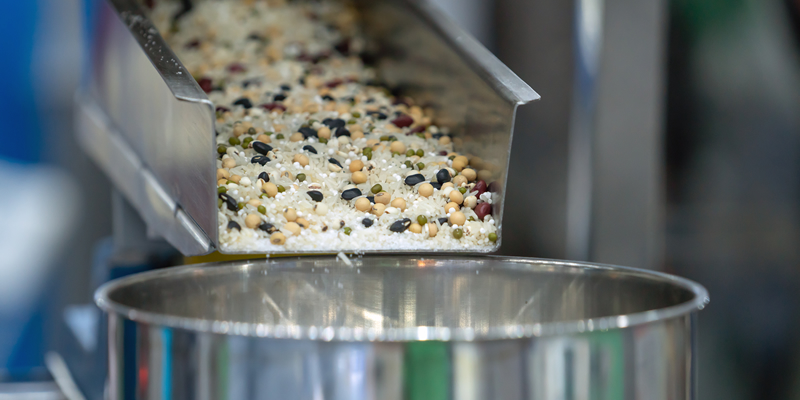
Regular maintenance recommendations
Maintenance Task | Description | Frequency |
---|---|---|
Cleaning | Clean blades and grinding chamber after each use to prevent residue buildup and bacteria growth. | After each use |
Lubrication | Apply food-grade lubricant to bearings and gears to reduce friction and wear. | Weekly |
Inspection | Check blade wear, fasteners, and other components for damage or loosening. | Monthly |
Electrical Check | Inspect cords, plugs, and control panels to prevent electrical hazards. | Monthly |
Calibration | Ensure the grinding fineness meets standards; adjust blades or screens. | Quarterly |
Dust Control | Clean the feed inlet and dust collection system to prevent dust from affecting performance. | Weekly |
Safety Inspection | Check protective devices and safety mechanisms to ensure proper function. | After each use |
- How to clean an industrial Milling Machines Properly:
- After each use, clean the milling machines immediately, especially the blades and the inside of the grinding chamber to prevent the accumulation of food residue and avoid the growth of corrosion and bacteria.
- Use warm water and neutral detergent to clean. Avoid using too harsh chemical detergents to avoid damaging the equipment.
- How to Lubricate Your Grinding Machines for Long-Term Efficiency:
- Regularly add lubricating oil to the moving parts of the crusher, especially bearings and gears, to reduce friction and wear.
- Choose food-grade lubricants suitable for food processing equipment to ensure safety and hygiene.
- How to Check and Maintain Grinder Components:
- Regularly check the wear of blades, hammers and other wearing parts, and replace worn parts in a timely manner.
- Check whether fasteners (such as bolts, nuts, etc.) are loose and retighten if necessary.
- Why Regular Electrical Inspections Are Crucial for Safety and Performance:
- Regularly check the condition of cords, plugs, and control panels to make sure they are not damaged or deteriorated.
- Check the motor and drive system to ensure normal operation and no abnormal noise or overheating.
- Why Proper Calibration Ensures Consistent Product Quality:
- Regularly check whether the grinding fineness meets the required standards. If discrepancies are found, adjust the blade spacing or replace components.
- Ensure that the screen is not clogged, as this can affect grinding performance.
- The Hidden Dangers of Poor Dust Control – How to Protect Your Equipment and Workplace:
- Ensure that dust collection devices (such as filter bags and fans) are functioning properly to prevent dust from affecting the working environment and machine lifespan.
- Clean any residue from the feed and discharge ports to prevent dust accumulation that could cause malfunctions.
- How to Conduct a Comprehensive Safety Inspection for Your Grinder:
- Ensure that all safety devices (such as protective covers and emergency stop buttons) are functioning properly to prevent accidents.
- Provide operators with appropriate protective equipment, such as gloves and safety goggles.
Repair suggestions
- Troubleshooting:
- If the pulverizer operates abnormally (such as abnormal noise, vibration, poor operation, etc.), first stop it for inspection and eliminate possible causes of the failure.
- Common problems such as material jamming, blade wear, motor overheating, etc. can be checked and simply dealt with according to the equipment instructions.
- Preventive Maintenance:
- Establish a regular inspection schedule to detect potential issues in advance and prevent unexpected equipment failures.
- Implement maintenance cycles (e.g., monthly, quarterly) for in-depth inspections, including internal components and lubrication conditions.
- Professional maintenance:
- When you encounter complex faults or problems that cannot be handled by yourself, you should contact professional maintenance personnel for repairs in time.
- When repairing, original parts or substitutes that meet specifications should be used to ensure the performance and safety of the equipment.
- Spare parts management:
- It is recommended that factories keep spare parts for common wearing parts (such as blades, screens, bearings, etc.) so that they can be replaced in time when needed to reduce downtime.
- Regularly check the inventory of spare parts to ensure sufficient spare parts.
- Component Upgrades & Retrofitting:
- Consider upgrading certain parts, such as more durable blades or energy-efficient motors, to improve performance and longevity.
- Depending on equipment usage, add extra safety features or automatic monitoring systems to enhance usability and safety.
- Logging and tracking:
- Establish equipment maintenance records and record in detail the content, time and replaced parts of each maintenance and repair to facilitate follow-up tracking and management.
- Based on the usage and maintenance records of the equipment, formulate and optimize maintenance plans to improve the operating efficiency and service life of the equipment.
- Emergency Repair Procedures:
- Set up emergency repair procedures to ensure operators can respond quickly to severe equipment failures, minimizing production impact.
- Assign designated personnel for urgent repairs and ensure that repair tools and spare parts are easily accessible.
Conclusion
Ensuring the optimal operation and longevity of a food grinder requires a proactive and systematic approach to maintenance. Regular cleaning prevents residue buildup and bacterial growth, while proper lubrication minimizes wear and tear on critical components. Routine inspections of blades, screens, and electrical systems help detect potential issues before they escalate into costly repairs. Beyond routine maintenance, keeping spare parts readily available and maintaining accurate service records can significantly reduce downtime and improve operational efficiency. Upgrading components when necessary and implementing emergency repair protocols further enhance equipment reliability. By adopting these best practices, businesses can maximize productivity, reduce operational costs, and maintain consistent product quality. Prioritizing regular maintenance not only safeguards your equipment investment but also ensures a safe and efficient production environment. Start implementing a structured maintenance plan today to keep your grinder running at peak performance!Article Classification
Recent Articles
- What is a Pin Mill? Understanding Its Working Principle, Advantages, and Uses!
- What is a Ribbon Mixer? Discover Its 3 Main Advantages and Applications
- How to Choose a Powder Grinder: Key Principles and 3 Major Applications for Boosting Production Efficiency
- How to Choose the Right Plastic Recycling Machine for Your Waste—Key Tips for Reduction!
- Understanding Hammer Mills: Operation, Advantages, Disadvantages, and Selection Criteria